DFMA® Resources
Success stories and implementation information that will help you
communicate the benefits of DFMA® within your organization, and to
quickly bring new users up to speed.
General
- What is DFMA®?
- DFMA® stands for Design for Manufacture and Assembly. It is a comprehensive approach to product design that integrates two key methodologies: Design for Assembly (DFA) and Design for Manufacture (DFM). DFMA® helps designers simplify product structure, reduce manufacturing and assembly costs, and improve product quality by considering both manufacturing and assembly from the outset. Developed by Dr. Geoffrey Boothroyd and Dr. Peter Dewhurst, DFMA® provides robust and intuitive tools for design and cost analysis, facilitating quicker and more accurate decision-making.
- What does DFMA® software do?
- DFMA® software is broken into two modules: Design for Assembly (DFA) and Design for Manufacture (DFM). DFA is a product structure analysis tool that focuses on simplifying the product structure by reducing the number of parts and making assembly processes easier and more efficient. DFM is a should-costing tool for parts that emphasizes designing parts for ease of manufacturing with the goal of minimizing production costs and improving quality. The software offers robust and intuitive tools for cost analysis, enabling early and accurate cost estimations and informed decision-making that balances cost, quality, and manufacturability.
- What industries/products does DFMA® software work best with?
- DFMA® can be applied to any electro-mechanical product that requires the manufacture and assembly of metallic or plastic components. Ignoring any cultural/organizational challenges, there is no evidence that DFMA® is better suited to any particular industry. It is highly versatile and can be used across a wide range of industries, including automotive, aerospace, electronics, consumer goods, and medical devices.
- Is DFA (Design for Assembly) an exercise in Value Engineering?
- While there are similarities between these two methodologies in that they both involve function and cost, it is intended that total product functionality be static during a Design for Assembly exercise. To achieve cost reduction through Design for Assembly, the use of fewer, multi-functional parts in place of more complicated assemblies is encouraged. Value Engineering differs in that product functionality is analyzed in terms of value delivered by its inclusion in the product. In Design for Assembly, we are only focused on impacting the product's assembly efficiency while maintaining all of the functionality the designer intended.
- Do you provide training that covers the DFMA® methodology but not the software?
- No, we do not offer training that does not also include the use of the DFMA® software. Although there are some basic “principles of DFMA” that can be learned, the methodology is data-driven and not practical to perform using hand calculations. DFMA® is not a brainstorming exercise but a systematic process for generating a superior product design. Due to the necessity of the data, the methodology and the software have co-existed in usage since enterprise software became prominent in the 1980s.
- What are the benefits of using DFMA®?
- DFMA® provides numerous benefits, including significant cost reductions, improved product quality, and streamlined manufacturing and assembly processes. By focusing on design optimization, DFMA® helps engineers identify and eliminate inefficiencies, leading to lower production costs and shorter time-to-market. Additionally, DFMA® promotes better collaboration between design and manufacturing teams, ensuring that products are designed with manufacturability in mind from the outset. This approach not only reduces the likelihood of costly redesigns but also improves overall product performance and reliability. By using DFMA®, companies can also achieve better resource utilization, reduce waste, and enhance sustainability efforts.
- Can DFMA® help in reducing time-to-market for new products?
- Yes, DFMA® can significantly reduce time-to-market for new products by identifying potential manufacturing and assembly issues early in the design process. By addressing these issues upfront, DFMA® minimizes the need for costly and time-consuming redesigns. Additionally, DFMA® promotes efficient and streamlined manufacturing processes, reducing lead times and accelerating product development. This approach allows companies to bring high-quality products to market faster, gaining a competitive edge and meeting customer demands more effectively. The proactive problem-solving capabilities of DFMA® ensure that products are optimized for manufacturability from the start, reducing delays and improving overall project timelines.
- How does DFMA® contribute to sustainability and environmental goals?
- DFMA® contributes to sustainability and environmental goals by promoting the efficient use of materials and resources. By optimizing product designs for manufacturability, DFMA® helps reduce material waste, energy consumption, and overall environmental impact. The methodology encourages the use of fewer parts, simpler assembly processes, and more sustainable materials, leading to greener manufacturing practices. Additionally, DFMA® supports the design of products that are easier to disassemble and recycle, further enhancing their environmental friendliness. Companies using DFMA® can achieve both economic and environmental benefits, aligning their product development strategies with sustainability goals.
Purchase/Licensing
- How much does the software cost?
- Due to the wide variety of needs from our customers, we require some information before we can prepare a quote for you. To begin the process, please visit the Contact Us page and fill out the required form. A representative from our organization should reach out to you shortly.
- What type of software licenses do you sell?
- We offer floating and node-locked licenses, both of which can be purchased as an annual subscription or perpetual license. A floating license is hosted by the customer on a server they control and has a defined number of simultaneous users. A node-license is locked to a specific computer/machine. Floating licenses provide greater flexibility in that they can be accessed by an unlimited number of different organizational users, only being restricted by the number of concurrent user licenses the organization has purchased. Node-locked licenses allow customers to use the software without a network connection, which is ideal for users who travel frequently.
- Do you offer a trial version of your software?
- Yes, at our discretion, we offer 30-day trial licenses with full functionality to eligible customers. This allows potential users to explore the software’s capabilities and determine if it meets their needs before committing to a purchase. To request a trial version, please contact our sales team through the Contact Us page.
- Do you offer a discount for academic institutions?
- Yes, we provide discounted pricing for eligible institutions that are interested in providing DFMA® related lab or coursework. Academic licenses are only sold as annual subscriptions. Please submit a Contact Us request to receive pricing information.
Software Usage
- Do you provide training to assist in learning how to use the software?
- Yes, we offer training hosted at our office in East Greenwich, RI, USA and on-site workshops. The training we host is typically conducted over two days, while on-site workshops are usually three-day events. Our training programs cover all aspects of the software, from basic functionality to advanced features, ensuring that users can effectively apply DFMA® principles in their work. Please refer to the Services page for more information.
- Is it necessary to have manufacturing expertise to use the DFMA® software?
- With regards to the DFA Product Simplification component, it is expected that a user who is not very familiar with manufacturing processes should not have any difficulty utilizing the software. In DFM Concurrent Costing® however, it is required that the user has at least some basic knowledge of the process being utilized in their part analysis. While DFM Concurrent Costing® builds a process chart and supplies default assumptions based on manual dimensions or a CAD model, there are often important cost drivers of the design that need to be further accounted for. DFM Concurrent Costing® makes it easy to do this, and the presentation of the cost driver inputs is a helpful learning tool for less experienced users.
- What manufacturing processes does your software cover?
- The primary manufacturing cost models contained in DFM Concurrent Costing® are Assembly Fabrication, Automatic Assembly, Blow Molding, Die Casting, Plastic Extrusion, Metal Extrusion, Hot Forging, Injection Molding, Investment Casting, Machining, PCBA, Sand Casting, Sheet Metal, Foam Molding, Powder Metals, and Thermoforming. Machining covers a large variety of machining methods and operations. Overall, these models cover the majority of manufacturing techniques, providing comprehensive support for various industries and applications.
- Where do you get your cost results data from?
- A common misconception is that our DFM Concurrent Costing® results must be referencing some form of historical pricing. The reality is that every DFM estimate is made "fresh." That is, every cost result is uniquely based on our knowledge of manufacturing science, which is applied to the geometry parameters the user has provided. The primary output of this effort is a cycle time, which can then be used in combination with other inputs such as material costs and machine/labor rates to provide a cost result. This practice usually provides significant accuracy advantages over historical pricing, and is much less reliant on us tracking market changes over time.
- Does your software come with data?
- Yes, in addition to the hard-coded data, there are four types of data libraries included. They are the material, operations, machines and process parameters libraries. We include one of these each for the two manufacturing profiles that are included. The included data provides everything you need to complete a DFA analysis or DFM cost estimate. All of the libraries are stored in XML format, which can be accessed and/or modified by other programs.
- How often do you update the data libraries used by the software?
- We evaluate the data libraries for updates several times a year. Our experience has taught us that manufacturing input costs, such as machine rates and operator rates, don’t change as quickly as our customers expect. Other inputs, such as the raw material prices, are typically negotiated at contract rates between the specific customer and their supplier. For organizations that seek to model more dramatic fluctuations, or need to model contract rates, there is substantial customization capability built into the DFMA® software. All of the data is accessible both from within the software and in .XML files that can be modified by other programs.
- Can the software take advantage of information from 3D CAD models?
- Yes, an integrated CAD import capability allows the user to use .step, .stp, .stl, or .iges CAD formats in their analysis. These are standard formats that almost every CAD package can export. The amount of information that can be used in an analysis depends on the application or the manufacturing process being analyzed. In DFA Product Simplification, only basic envelope dimensions are useful. In DFM Concurrent Costing®, cost driver information for many processes can be automatically utilized. Other geometry information can be selected directly on the model by the user.
- Should I expect a supplier quote to match the cost estimate I generate in DFM Concurrent Costing®?
- Whether a DFM estimate is supposed to “match” the supplier quote is highly subjective. The cost results of DFM Concurrent Costing® are meant to represent the manufacturing cost burden to a supplier. The market forces that determine the actual price that a supplier will charge are different. Generally, it is our expectation that a gap will exist between the DFM estimate and the quote the supplier provides. Assuming a DFM part analysis is consistent with the manufacturing practices employed by the supplier, the estimate is an excellent guide in determining cost reduction potential from engaging in supplier negotiation.
- What kind of support is available if I encounter issues while using the software?
- We offer comprehensive support services to assist users with any issues they may encounter while using the software. Our support options include online resources such as user manuals, and video tutorials, as well as direct support through email and phone. Our technical support team is staffed with experienced professionals who can provide guidance and troubleshooting for a wide range of issues. Our goal is to ensure that users have the resources and support they need to use the software effectively.
- Can DFMA® software be customized to fit specific industry needs?
- Yes, DFMA® software is highly customizable and can be tailored to meet the specific needs of different industries and applications. Customization options include configuring the software to handle specific manufacturing processes, integrating industry-specific data libraries, and developing custom reports and analysis tools. Our team of experts works closely with customers to understand their unique requirements and implement solutions that maximize the value of DFMA® in their specific context. Whether you are in aerospace, automotive, electronics, or any other industry, DFMA® can be adapted to address your particular challenges and goals.
- How long does it typically take to become proficient in using DFMA® software?
- The time to proficiency varies based on individual experience, the complexity of the projects, and the level of training undertaken. For most users, becoming proficient in using DFMA® software can take a few weeks to a few months. Our comprehensive training programs, which include online courses, in-person workshops, and on-site training, are designed to accelerate the learning process. These programs cover all aspects of the software, from basic functionality to advanced features, ensuring that users can effectively apply DFMA® principles in their work. Continuous practice and participation in the user community can further enhance proficiency and expertise.
Technical
- What are the system requirements for your software?
- Please refer to the bottom of our Support Page for PC system requirements. This page provides detailed information on the hardware and software specifications needed to run DFMA® software effectively. Ensuring that your system meets these requirements will help you achieve optimal performance and avoid potential issues.
- Does your software use a database?
- No, the software does not have a central database where analysis data is stored. Each analysis is a separate DFA or DFM file that can contain numerous parts or products. The only centralized data storage is in the material, machine, operations, and process parameters libraries. These libraries do not keep track of any user-generated analysis data. This decentralized approach provides flexibility and allows users to manage their analysis files independently.
- Does Boothroyd Dewhurst, Inc. monitor or have any form of access to user activity/data?
- No, there is no line of communication between the DFMA® software and Boothroyd Dewhurst, Inc. We only have access to analysis files or libraries if the user provides them to us as part of a support inquiry. We usually sign NDAs (Non-Disclosure Agreements) with organizations that request such support. User privacy and data security are of utmost importance to us, and we take all necessary measures to protect the confidentiality of user data.
- Can DFMA® software be deployed as a cloud application?
- Yes, the data libraries used by the software and the license server can both be accessed from cloud locations. Additionally, the software can be run in many virtualization environments. Please note that Boothroyd Dewhurst, Inc. does not currently participate in or provide active support for any such deployment. However, we can provide guidance on setting up cloud deployments and ensuring compatibility with cloud-based infrastructure.
Learn more about the DFMA methodology and the key definitions and benefits.
more >
View videos of all previously conducted webinars
more >
Customer stories on the use of DFMA® to improve their products and
development process.
more >
How to Use Design for Manufacture and Assembly to Slash
Manufacturing Overhead, Make Products Competitive, and Bring New
Efficiencies to the Manufacturing Process.
Specifically written for executive management to raise awareness
of the business benefits of implementing DFMA® in the product
development process.
more >
These are hype-free, factual slides which cover issues of
interest to top executives. If you are trying to communicate the
benefits of DFMA® to your company, use all or any of these slides.
They make a compelling case for using DFMA® to improve quality, lower
part count, decrease costs, facilitate cross-functional efficiency,
and get to market faster--all from an executive management point of
view.
more >
Leading manufacturers discuss the extended effects of early
design decisions on disciplines and departments at the other end of
their organizations. in the survey table, and in the comments from
participants, you will learn what they strive to accomplish and what
they have measured in savings from factory floor space to end‐of
life costs.
more >
A collection of technical papers representing the most successful
approaches to implementing DFMA® presented at the annual
International Forum on Design for Manufacture and Assembly.
more >
Quotations on the use of DFMA® from some of the world's most
respected companies.
more >
2024 papers and presentations
2020 virtual event on YouTube
2019 papers and presentations
2018 papers and presentations
2017 papers and presentations
2016 papers and presentations
2015 papers and presentations
2014 papers and presentations
2013 papers and presentations
2012 papers and presentations
|
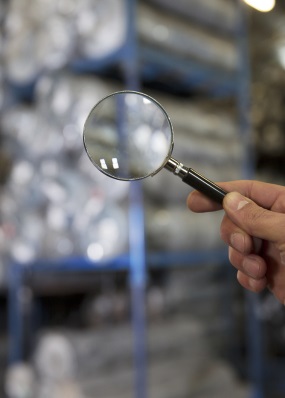 |